Dicing Machines
What are your requirements?
Dicing machines
We specialise in the design and manufacture of high precision dicing machines. Our machines are engineered for optimal quality, efficiency, and reliability, making sure you achieve the best results for your projects. Whether you are in the semiconductor, electronics, or photonics industry, our comprehensive range of dicing machines is tailored to meet your requirements.
Choosing the right machine
In the rapidly evolving world of semiconductors, photonics, and the electrical sectors, selecting the correct dicing machine for your needs can make all the difference when it comes to product quality and efficiency. Selecting a machine tailored to your specific needs not only ensures reliability of your components but can also increase production capabilities.
NEW ERA OF DICING: OUR BRAND-NEW DICING MACHINES!
-1.png?width=1414&height=1535&name=Untitled%20design%20(6)-1.png)
MicroAce Pro
The MicroAce Pro is a newly developed 6” semi-automatic dicing saw, equipped with a 2.2kW spindle as standard, while other spindle configurations are also available to suit a variety of applications including thick substrate cutting. The MicroAce Pro is suitable for a wide range of applications, not limited to silicon wafer dicing. It offers a high level of configurability to ensure optimal performance for your specific application.
This machine has a very small footprint. It features an auto-alignment function, auto kerf check function, self-adjustment function, and fragment shape recognition function.
The performance of the MicroAce Pro is underpinned by a new Loadpoint NanoControl control system, which is equipped with a user-friendly 17" LCD touch screen and operated through an intuitive new user interface.
This machine has a very small footprint. It features an auto-alignment function, auto kerf check function, self-adjustment function, and fragment shape recognition function.
The performance of the MicroAce Pro is underpinned by a new Loadpoint NanoControl control system, which is equipped with a user-friendly 17" LCD touch screen and operated through an intuitive new user interface.
-1.png?width=1384&height=1570&name=Untitled%20design%20(20)-1.png)
NanoAce Duo Pro
The NanoAce Duo Pro is a newly developed 12” semi-automatic dicing saw, equipped with two facing spindles that can simultaneously dice workpieces at high throughput, a vision alignment system and high resolution closed loop linear positioning encoders in Y axes where high performance tolerances are required.
This machine has a very small footprint compared to its equivalents. It features an auto-alignment function, auto kerf check function, self-adjustment function, and statistical analysis function. A high-power spindle is also available for this machine.
The performance of the NanoAce Duo Pro is underpinned by a new Loadpoint NanoControl control system, which is equipped with a user-friendly 17" LCD touchscreen and operated through an intuitive new user interface.
This machine has a very small footprint compared to its equivalents. It features an auto-alignment function, auto kerf check function, self-adjustment function, and statistical analysis function. A high-power spindle is also available for this machine.
The performance of the NanoAce Duo Pro is underpinned by a new Loadpoint NanoControl control system, which is equipped with a user-friendly 17" LCD touchscreen and operated through an intuitive new user interface.
-1.png?width=1321&height=1326&name=Untitled%20design%20(8)-1.png)
NanoAce Fully Automatic Duo Pro
The NanoAce Fully Automatic Duo Pro is a newly developed 12" fully automatic dicing saw, equipped with two facing spindles that can dice workpieces simultaneously at high throughput, a vision alignment system and high resolution closed loop linear positioning encoders in Y axes where high performance tolerances are required.
This machine is highly cost-effective due to its rapid dicing speed and fully automated operation. It features an auto-alignment function, auto kerf check function, self-adjustment function, and statistical analysis function. A high-power spindle is also available for this machine.
The performance of the NanoAce Fully Automatic Duo Pro is underpinned by a new Loadpoint NanoControl control system, which is equipped with a user-friendly 17" LCD touch screen and operated through an intuitive new user interface.
This machine is highly cost-effective due to its rapid dicing speed and fully automated operation. It features an auto-alignment function, auto kerf check function, self-adjustment function, and statistical analysis function. A high-power spindle is also available for this machine.
The performance of the NanoAce Fully Automatic Duo Pro is underpinned by a new Loadpoint NanoControl control system, which is equipped with a user-friendly 17" LCD touch screen and operated through an intuitive new user interface.
Sustained Excellence: Our Classic Dicing Machines!
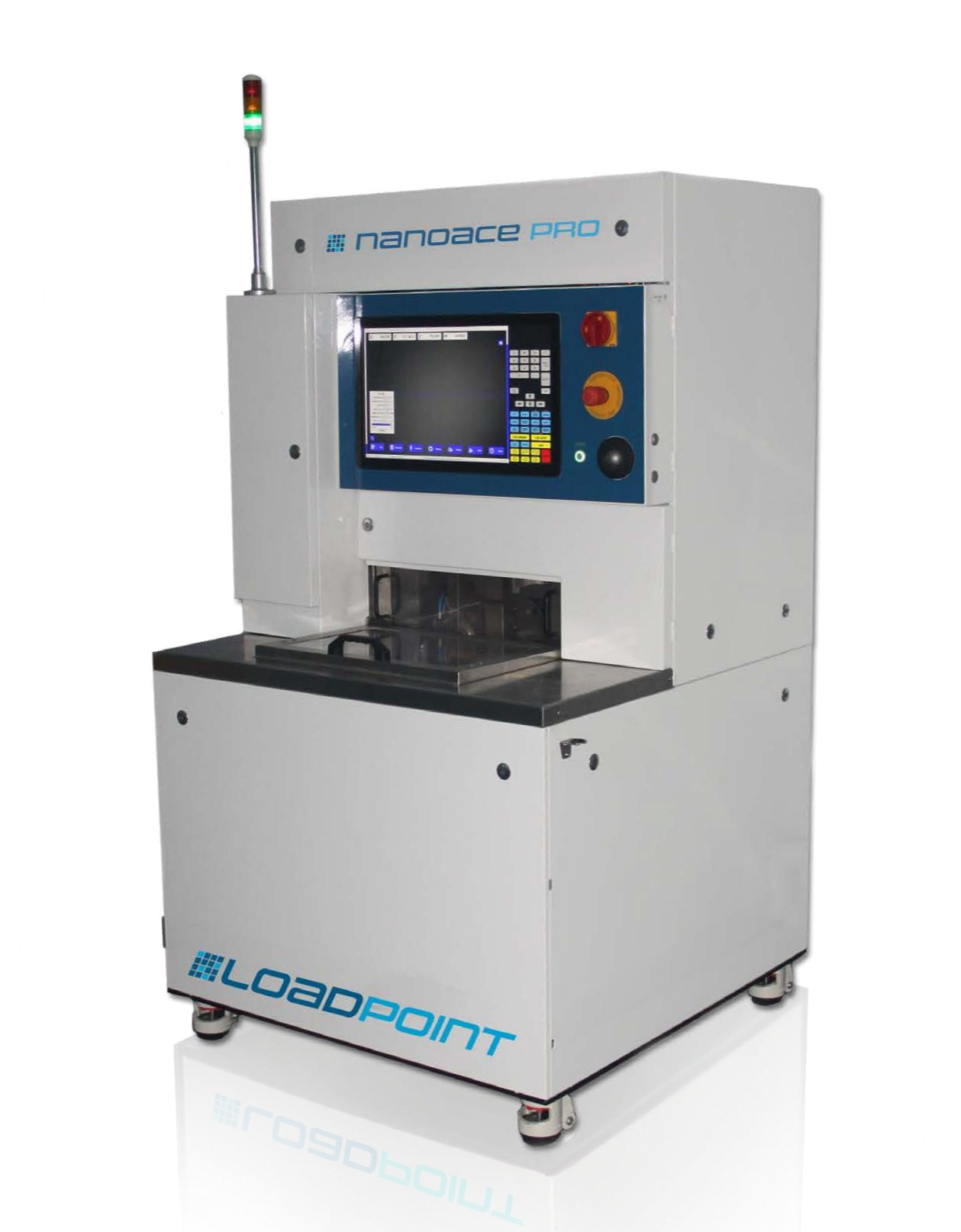
NanoAce Pro
The NanoAce Pro is a 12” dicing saw that also serves many applications in larger area substrate cutting and dicing. The NanoAce Pro is an automatic dicing saw with vision alignment system and high resolution closed loop linear positioning encoders in all axes where high performance tolerances are required. They offer a high level of configurability that allows the machine to be optimised to suit the application.
The performance of the NanoAce is underpinned by the Loadpoint NanoControl control system now fitted with user friendly touch screen interface.
NanoControl can be developed bespoke to a customer’s application. This could involve taking the hassle out of calculating complex cut patterns or easy generation of 3D cutting profiles.
The performance of the NanoAce is underpinned by the Loadpoint NanoControl control system now fitted with user friendly touch screen interface.
NanoControl can be developed bespoke to a customer’s application. This could involve taking the hassle out of calculating complex cut patterns or easy generation of 3D cutting profiles.
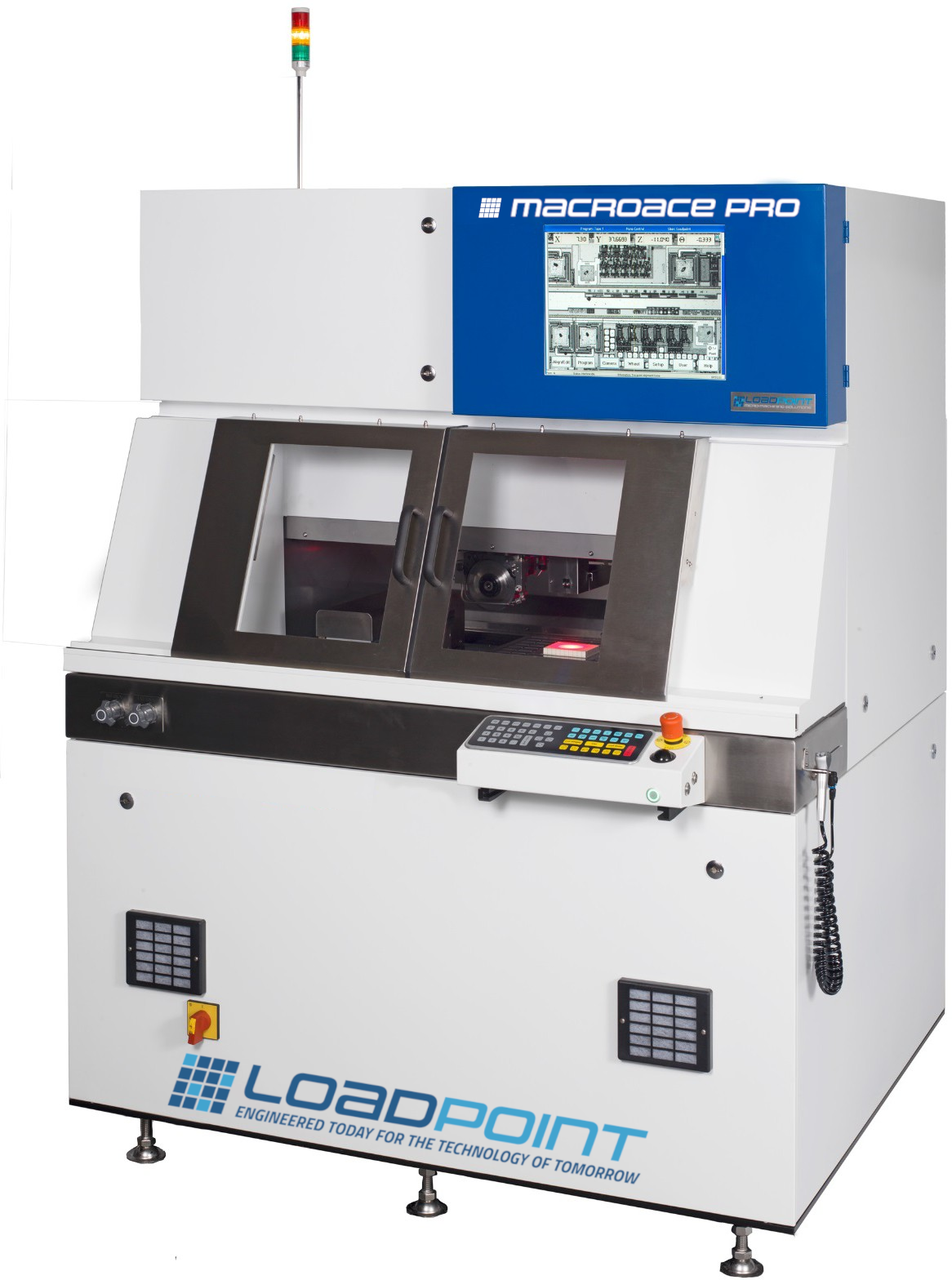
MacroAce Pro
MacroAce Pro for heavier duty applications requiring high power spindle delivery and large work areas.
The MacroAce II offers a unique combination of dicing machine performance with CNC-like power and work area capability. The spindle’s drive profile has been optimised to give maximum 3KW power delivery in the 1,000 – 10,000rpm range, exactly where it is required for heavier duty ceramic and metal cutting applications.
Additionally, cut depths of up to 55mm with cut lengths of up to 450mm help make the MacroAce II a best-in-class leader. The MacroAce Pro is frequently the first-choice system for cutting bulk ceramics and lower frequency PZT sonar arrays.
The performance of the MacroAce Pro is underpinned by the Loadpoint NanoControl control system; a common control platform used across all our machines. Another feature of NanoControl is that it can be developed bespoke to a customer’s application.
This could involve taking the hassle out of calculating complex cut patterns or easy generation of 3D cutting profiles.
The MacroAce II offers a unique combination of dicing machine performance with CNC-like power and work area capability. The spindle’s drive profile has been optimised to give maximum 3KW power delivery in the 1,000 – 10,000rpm range, exactly where it is required for heavier duty ceramic and metal cutting applications.
Additionally, cut depths of up to 55mm with cut lengths of up to 450mm help make the MacroAce II a best-in-class leader. The MacroAce Pro is frequently the first-choice system for cutting bulk ceramics and lower frequency PZT sonar arrays.
The performance of the MacroAce Pro is underpinned by the Loadpoint NanoControl control system; a common control platform used across all our machines. Another feature of NanoControl is that it can be developed bespoke to a customer’s application.
This could involve taking the hassle out of calculating complex cut patterns or easy generation of 3D cutting profiles.